Wybór odpowiedniej destylarki do rozpuszczalników jest kluczowy dla uzyskania wysokiej jakości produktów. Na rynku dostępnych…
Destylarka do rozpuszczalników to urządzenie, które wykorzystuje proces destylacji do oddzielania różnych substancji chemicznych. Działa na zasadzie podgrzewania mieszaniny, co powoduje odparowanie substancji o niższej temperaturze wrzenia, a następnie skraplania pary w celu uzyskania czystego rozpuszczalnika. W praktyce oznacza to, że destylarka może być używana do odzyskiwania rozpuszczalników organicznych, takich jak etanol czy aceton, co jest szczególnie przydatne w laboratoriach chemicznych oraz w przemyśle. Dzięki temu procesowi można nie tylko zaoszczędzić na kosztach zakupu nowych rozpuszczalników, ale także zredukować ilość odpadów chemicznych, co jest korzystne dla środowiska. Warto również zauważyć, że destylarki są dostępne w różnych rozmiarach i konfiguracjach, co pozwala na ich dostosowanie do specyficznych potrzeb użytkowników.
Jakie są rodzaje destylarek do rozpuszczalników dostępnych na rynku
Na rynku dostępnych jest wiele rodzajów destylarek do rozpuszczalników, które różnią się zarówno konstrukcją, jak i przeznaczeniem. Jednym z najpopularniejszych typów są destylarki laboratoryjne, które charakteryzują się precyzyjnym działaniem i możliwością regulacji temperatury. Takie urządzenia często wyposażone są w dodatkowe elementy, takie jak chłodnice czy kolumny frakcyjne, które zwiększają efektywność procesu destylacji. Innym rodzajem są destylarki przemysłowe, które są znacznie większe i przeznaczone do masowej produkcji czystych rozpuszczalników. Te urządzenia muszą spełniać rygorystyczne normy bezpieczeństwa oraz wydajności. Istnieją również przenośne destylarki, które mogą być używane w terenie lub w mniejszych laboratoriach. Wybór odpowiedniej destylarki zależy od wielu czynników, takich jak rodzaj przetwarzanych substancji, wymagania dotyczące czystości oraz dostępna przestrzeń robocza.
Jakie są korzyści z używania destylarki do rozpuszczalników w laboratoriach
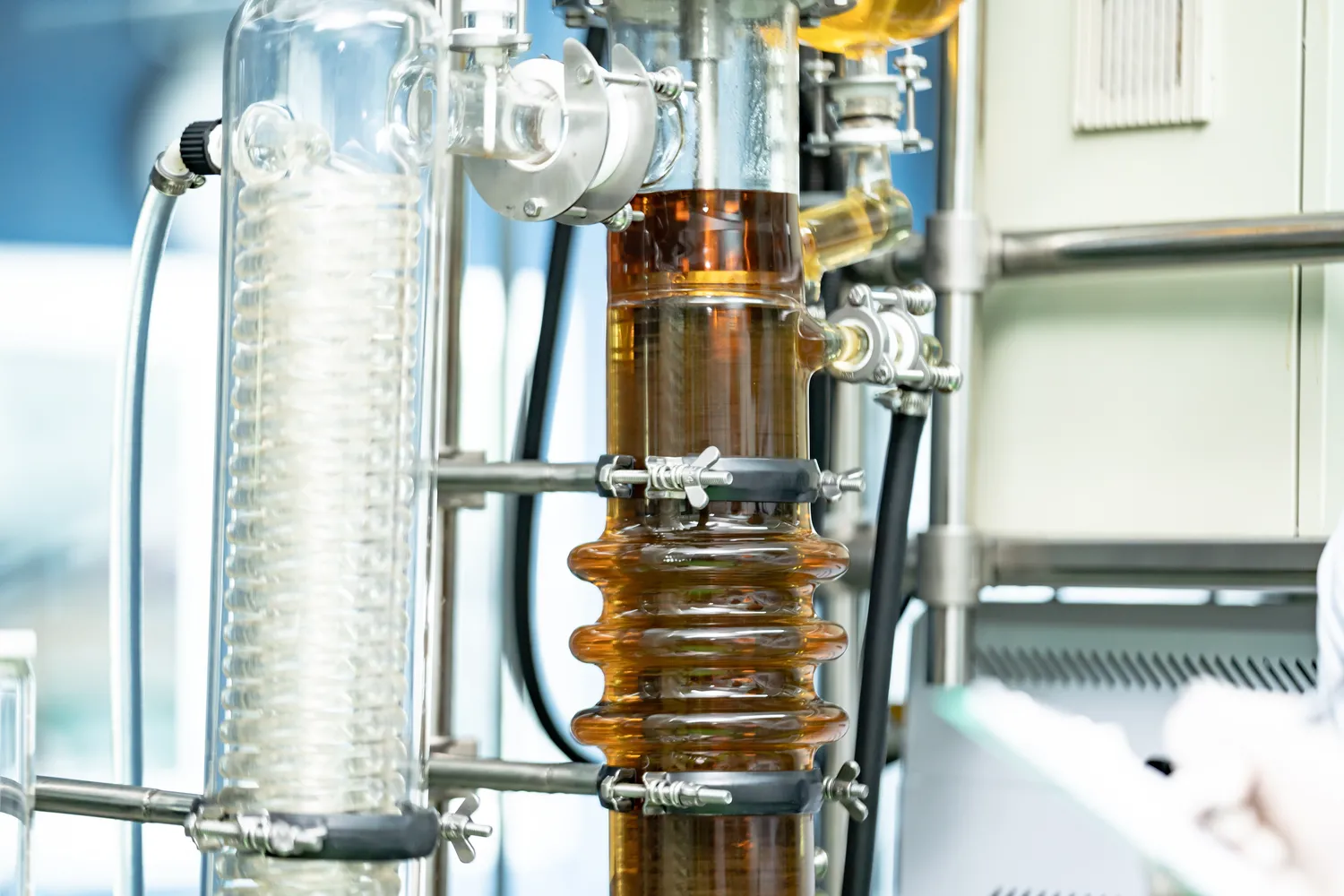
Korzystanie z destylarki do rozpuszczalników w laboratoriach niesie ze sobą wiele korzyści. Przede wszystkim umożliwia efektywne odzyskiwanie cennych substancji chemicznych, co przekłada się na oszczędności finansowe oraz zmniejszenie wpływu na środowisko. Dzięki możliwości wielokrotnego użycia tych samych rozpuszczalników laboratoria mogą znacznie ograniczyć ilość odpadów chemicznych generowanych podczas pracy. Ponadto proces destylacji pozwala na uzyskanie wysokiej czystości substancji, co jest kluczowe w wielu eksperymentach i analizach chemicznych. Użycie destylarki zwiększa także bezpieczeństwo pracy w laboratoriach poprzez minimalizację ryzyka związane z przechowywaniem dużych ilości niebezpiecznych substancji chemicznych. Dodatkowo nowoczesne modele destylarek często wyposażone są w systemy automatyzacji oraz monitoring temperatury i ciśnienia, co ułatwia pracę i zwiększa jej efektywność.
Jakie czynniki należy wziąć pod uwagę przy wyborze destylarki do rozpuszczalników
Wybór odpowiedniej destylarki do rozpuszczalników wymaga uwzględnienia kilku kluczowych czynników. Przede wszystkim należy zastanowić się nad rodzajem substancji chemicznych, które będą przetwarzane. Różne materiały mają różne temperatury wrzenia oraz właściwości fizykochemiczne, co może wpłynąć na wybór konkretnego modelu urządzenia. Kolejnym istotnym aspektem jest wydajność destylarki – im większa wydajność, tym szybciej można odzyskać potrzebny rozpuszczalnik. Ważne jest także zwrócenie uwagi na jakość materiałów użytych do budowy urządzenia; stal nierdzewna czy szkło borokrzemowe to materiały zapewniające długowieczność i odporność na działanie agresywnych substancji chemicznych. Należy również pomyśleć o przestrzeni roboczej – niektóre modele zajmują więcej miejsca niż inne, co może być problematyczne w mniejszych laboratoriach.
Jakie są najczęstsze błędy przy używaniu destylarki do rozpuszczalników
Podczas korzystania z destylarki do rozpuszczalników, wiele osób popełnia typowe błędy, które mogą prowadzić do nieefektywności procesu lub nawet uszkodzenia urządzenia. Jednym z najczęstszych błędów jest niewłaściwe ustawienie temperatury. Zbyt wysoka temperatura może prowadzić do przegrzania substancji, co skutkuje ich degradacją oraz powstawaniem niepożądanych produktów ubocznych. Z kolei zbyt niska temperatura może uniemożliwić skuteczne odparowanie rozpuszczalnika. Kolejnym problemem jest nieodpowiednia kalibracja sprzętu; regularne sprawdzanie i dostosowywanie parametrów pracy destylarki jest kluczowe dla uzyskania optymalnych wyników. Niezwykle ważne jest także dbanie o czystość urządzenia – resztki poprzednich substancji mogą zanieczyścić nowo przetwarzany rozpuszczalnik, co wpływa na jego jakość. Warto również pamiętać o odpowiednim zabezpieczeniu miejsca pracy; brak wentylacji lub niewłaściwe przechowywanie substancji chemicznych mogą prowadzić do niebezpiecznych sytuacji.
Jakie są zasady bezpieczeństwa przy pracy z destylarką do rozpuszczalników
Praca z destylarką do rozpuszczalników wiąże się z pewnym ryzykiem, dlatego przestrzeganie zasad bezpieczeństwa jest kluczowe dla ochrony zdrowia i życia osób pracujących w laboratoriach. Przede wszystkim należy zawsze nosić odpowiednią odzież ochronną, taką jak rękawice, gogle oraz fartuchy laboratoryjne, które chronią przed kontaktem z chemikaliami. Ważne jest także zapewnienie odpowiedniej wentylacji w pomieszczeniu, w którym znajduje się destylarka; opary chemiczne mogą być szkodliwe dla zdrowia, dlatego warto korzystać z wyciągów lub wentylatorów. Kolejną istotną zasadą jest unikanie kontaktu źródeł ciepła z łatwopalnymi substancjami; należy zachować szczególną ostrożność podczas podgrzewania mieszanin oraz trzymać materiały palne z dala od urządzenia. Warto również regularnie kontrolować stan techniczny destylarki i jej elementów, aby upewnić się, że nie ma żadnych uszkodzeń mogących prowadzić do wycieków czy awarii. Należy także być świadomym procedur awaryjnych oraz lokalizacji sprzętu gaśniczego w przypadku wystąpienia pożaru lub innego zagrożenia.
Jakie są różnice między destylacją prostą a frakcyjną w kontekście destylarki do rozpuszczalników
Destylacja prosta i frakcyjna to dwa podstawowe procesy stosowane w destylacji rozpuszczalników, które różnią się zarówno metodologią, jak i zastosowaniem. Destylacja prosta polega na podgrzewaniu cieczy do momentu jej odparowania i skraplaniu pary w celu uzyskania czystego rozpuszczalnika. Ten proces jest stosunkowo prosty i efektywny w przypadku substancji o znacznie różniących się temperaturach wrzenia. Jednak gdy składniki mają podobne temperatury wrzenia, destylacja prosta staje się mniej efektywna. W takich przypadkach lepszym rozwiązaniem jest destylacja frakcyjna, która wykorzystuje kolumnę frakcyjną do oddzielania składników na podstawie ich różnych temperatur wrzenia. Kolumna ta pozwala na wielokrotne skraplanie i odparowywanie pary, co zwiększa czystość uzyskanego produktu końcowego. W praktyce oznacza to, że destylacja frakcyjna jest bardziej skomplikowana i wymaga bardziej zaawansowanego sprzętu, ale pozwala na uzyskanie wyższej jakości rozpuszczalników.
Jakie są koszty eksploatacji destylarki do rozpuszczalników
Koszty eksploatacji destylarki do rozpuszczalników mogą się znacznie różnić w zależności od wielu czynników, takich jak typ urządzenia, jego wydajność oraz częstotliwość użytkowania. Podstawowym kosztem jest energia potrzebna do podgrzewania cieczy; im większa moc urządzenia oraz im dłużej pracuje, tym wyższe będą rachunki za prąd. Dodatkowo należy uwzględnić koszty związane z konserwacją i serwisowaniem sprzętu; regularne przeglądy techniczne są niezbędne dla zapewnienia prawidłowego działania oraz bezpieczeństwa użytkowania destylarki. Koszty zakupu materiałów eksploatacyjnych również mogą być znaczące; filtry czy elementy chłodzące wymagają okresowej wymiany, co generuje dodatkowe wydatki. Warto również pamiętać o kosztach związanych z utylizacją odpadów chemicznych powstających podczas procesu destylacji; odpowiednie zarządzanie tymi materiałami jest kluczowe dla ochrony środowiska oraz zgodności z przepisami prawa.
Jakie innowacje technologiczne wpływają na rozwój destylarek do rozpuszczalników
W ostatnich latach rozwój technologii znacząco wpłynął na konstrukcję i funkcjonalność destylarek do rozpuszczalników. Nowoczesne modele często wyposażone są w zaawansowane systemy automatyzacji, które umożliwiają precyzyjne kontrolowanie parametrów pracy urządzenia bez konieczności stałego nadzoru ze strony operatora. Dzięki temu można osiągnąć wyższą efektywność procesu oraz zmniejszyć ryzyko błędów ludzkich. Innowacyjne rozwiązania obejmują także zastosowanie inteligentnych czujników monitorujących temperaturę i ciśnienie w czasie rzeczywistym, co pozwala na szybką reakcję w przypadku wystąpienia nieprawidłowości. Ponadto coraz większą rolę odgrywają materiały kompozytowe oraz nanotechnologia, które zwiększają odporność urządzeń na działanie agresywnych substancji chemicznych oraz poprawiają ich wydajność energetyczną. Warto również zauważyć rosnącą popularność ekologicznych technologii odzysku rozpuszczalników, które minimalizują negatywny wpływ na środowisko naturalne poprzez zmniejszenie ilości odpadów chemicznych generowanych podczas procesu produkcji.
Jakie są najlepsze praktyki dotyczące konserwacji destylarki do rozpuszczalników
Aby zapewnić długowieczność i efektywność działania destylarki do rozpuszczalników, ważne jest przestrzeganie najlepszych praktyk dotyczących konserwacji tego typu urządzeń. Regularne czyszczenie wszystkich elementów roboczych powinno być priorytetem; resztki substancji chemicznych mogą prowadzić do korozji lub osadów, które wpływają na jakość końcowego produktu. Należy również systematycznie sprawdzać szczelność połączeń oraz stan uszczelek; wszelkie nieszczelności mogą prowadzić do utraty cennych substancji lub nawet zagrożeń dla zdrowia operatora. Kolejnym krokiem jest kontrola systemu chłodzenia – jego prawidłowe działanie jest kluczowe dla skutecznej pracy destylarki i zapobiegania przegrzewaniu się urządzenia. Warto także regularnie kalibrować sprzęt zgodnie z zaleceniami producenta; precyzyjna regulacja parametrów pracy pozwala na optymalne wykorzystanie możliwości urządzenia.