Budowa maszyn przemysłowych na zamówienie to proces, który wymaga starannego planowania oraz realizacji. Kluczowym etapem…
Budowa maszyn pneumatycznych opiera się na kilku kluczowych elementach, które współpracują ze sobą w celu efektywnego wykorzystania energii sprężonego powietrza. Na początku warto zwrócić uwagę na kompresor, który jest sercem całego systemu. Jego zadaniem jest sprężanie powietrza i dostarczanie go do reszty układu. Kompresory mogą być różnego rodzaju, od tłokowych po śrubowe, a ich wybór zależy od specyfiki zastosowania. Kolejnym istotnym elementem są zbiorniki ciśnieniowe, które magazynują sprężone powietrze i zapewniają stabilność ciśnienia w systemie. Zbiorniki te muszą być odpowiednio zaprojektowane, aby wytrzymać wysokie ciśnienie oraz korozję. Również nie można zapomnieć o zaworach, które kontrolują przepływ powietrza w systemie. W zależności od potrzeb mogą to być zawory elektromagnetyczne, ręczne lub automatyczne. Ostatnim kluczowym elementem są siłowniki pneumatyczne, które przekształcają energię sprężonego powietrza w ruch mechaniczny, co pozwala na wykonywanie różnorodnych prac.
Jakie są zastosowania maszyn pneumatycznych w przemyśle
Maszyny pneumatyczne znajdują szerokie zastosowanie w różnych dziedzinach przemysłu, co czyni je niezwykle wszechstronnymi narzędziami. W przemyśle produkcyjnym wykorzystuje się je do automatyzacji procesów montażowych oraz pakowania produktów. Dzięki swojej szybkości i precyzji, maszyny te znacznie zwiększają wydajność linii produkcyjnych. W branży motoryzacyjnej pneumatyka jest wykorzystywana do napędu narzędzi ręcznych, takich jak wkrętarki czy młoty udarowe, co ułatwia pracę i zwiększa komfort użytkowników. W sektorze spożywczym maszyny pneumatyczne służą do transportu materiałów sypkich oraz płynów, a także do pakowania żywności w atmosferze ochronnej. W medycynie natomiast stosuje się je do zasilania urządzeń diagnostycznych oraz chirurgicznych, co podnosi standardy bezpieczeństwa i efektywności zabiegów. W logistyce maszyny pneumatyczne są wykorzystywane do podnoszenia i transportu ciężkich ładunków, co znacząco zmniejsza ryzyko urazów w miejscu pracy.
Jakie są zalety i wady maszyn pneumatycznych
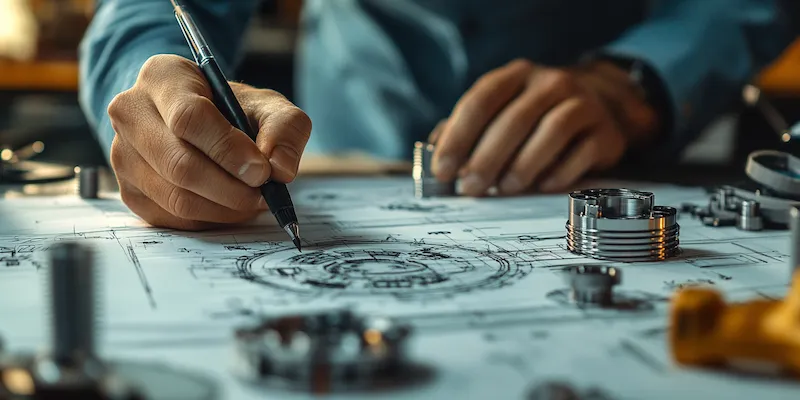
Budowa maszyn pneumatycznych wiąże się z wieloma zaletami, ale również pewnymi wadami, które warto rozważyć przed podjęciem decyzji o ich zastosowaniu. Do głównych zalet należy zaliczyć prostotę konstrukcji oraz łatwość w obsłudze. Maszyny te charakteryzują się niską wagą i kompaktowymi wymiarami, co ułatwia ich integrację w różnych środowiskach pracy. Ponadto, systemy pneumatyczne są mniej podatne na uszkodzenia mechaniczne niż ich elektryczne odpowiedniki, co przekłada się na niższe koszty eksploatacji i konserwacji. Kolejnym atutem jest możliwość pracy w trudnych warunkach, takich jak wysokie temperatury czy obecność wilgoci. Z drugiej strony, istnieją również pewne ograniczenia związane z używaniem maszyn pneumatycznych. Jednym z nich jest konieczność posiadania źródła sprężonego powietrza oraz odpowiednich instalacji do jego dystrybucji. Dodatkowo, efektywność energetyczna systemów pneumatycznych może być niższa niż w przypadku innych technologii napędowych, co wpływa na koszty operacyjne w dłuższym okresie czasu.
Jakie są nowoczesne technologie w budowie maszyn pneumatycznych
W ostatnich latach budowa maszyn pneumatycznych została wzbogacona o nowoczesne technologie, które znacząco poprawiają ich wydajność oraz funkcjonalność. Jednym z najważniejszych trendów jest automatyzacja procesów związanych z obsługą maszyn pneumatycznych. Dzięki zastosowaniu zaawansowanych systemów sterowania oraz czujników możliwe jest monitorowanie pracy urządzeń w czasie rzeczywistym oraz optymalizacja ich działania na podstawie zebranych danych. Wprowadzenie technologii Internetu Rzeczy (IoT) pozwala na zdalne zarządzanie maszynami oraz diagnostykę ich stanu technicznego bez potrzeby fizycznej obecności operatora. Innym istotnym kierunkiem rozwoju jest miniaturyzacja komponentów pneumatycznych, co umożliwia tworzenie bardziej kompaktowych i wydajnych układów napędowych. Nowoczesne materiały stosowane przy produkcji siłowników czy zaworów zwiększają ich trwałość oraz odporność na ekstremalne warunki pracy. Również rozwój technologii druku 3D otwiera nowe możliwości projektowania i produkcji elementów maszyn pneumatycznych na zamówienie, co przyspiesza procesy prototypowania i wdrażania innowacji na rynek.
Jakie są kluczowe czynniki wpływające na wydajność maszyn pneumatycznych
Wydajność maszyn pneumatycznych jest kluczowym czynnikiem, który wpływa na efektywność całego procesu produkcyjnego. Istnieje wiele czynników, które mogą mieć znaczący wpływ na działanie tych urządzeń. Przede wszystkim, jakość sprężonego powietrza odgrywa fundamentalną rolę w funkcjonowaniu systemu pneumatycznego. Zanieczyszczenia, takie jak woda, olej czy cząstki stałe, mogą prowadzić do uszkodzenia komponentów oraz obniżenia efektywności pracy. Dlatego ważne jest, aby stosować odpowiednie filtry i osuszacze, które zapewnią czystość powietrza. Kolejnym istotnym aspektem jest ciśnienie robocze. Utrzymywanie optymalnego ciśnienia pozwala na maksymalne wykorzystanie potencjału maszyn i minimalizuje ryzyko awarii. Warto również zwrócić uwagę na dobór odpowiednich komponentów do konkretnego zastosowania. Nieodpowiednie siłowniki czy zawory mogą prowadzić do spadku wydajności całego systemu. Oprócz tego, regularna konserwacja i przeglądy techniczne są niezbędne do utrzymania maszyn w dobrym stanie i zapewnienia ich długotrwałej pracy.
Jakie są różnice między maszynami pneumatycznymi a hydraulicznymi
Maszyny pneumatyczne i hydrauliczne to dwa różne typy systemów napędowych, które mają swoje unikalne cechy oraz zastosowania. Podstawową różnicą między nimi jest medium robocze – w przypadku maszyn pneumatycznych jest to sprężone powietrze, natomiast w hydraulicznych używa się cieczy, najczęściej oleju hydraulicznego. Ta różnica wpływa na wiele aspektów działania obu systemów. Maszyny pneumatyczne charakteryzują się szybką reakcją i dużą prędkością działania, co sprawia, że są idealne do zastosowań wymagających dynamicznych ruchów. Z kolei maszyny hydrauliczne oferują większą siłę i moment obrotowy, co czyni je bardziej odpowiednimi do zadań wymagających dużych obciążeń. W kontekście kosztów eksploatacji, systemy pneumatyczne są zazwyczaj tańsze w utrzymaniu ze względu na prostszą konstrukcję i mniejsze ryzyko wycieków. Jednakże maszyny hydrauliczne mogą być bardziej efektywne w przypadku długotrwałych operacji wymagających dużej mocy. Warto również zauważyć, że maszyny pneumatyczne są mniej podatne na uszkodzenia w trudnych warunkach atmosferycznych, takich jak wysoka wilgotność czy zanieczyszczenia chemiczne.
Jakie są najczęstsze problemy związane z maszynami pneumatycznymi
Podczas eksploatacji maszyn pneumatycznych mogą wystąpić różnorodne problemy, które mogą wpłynąć na ich wydajność oraz niezawodność. Jednym z najczęstszych problemów jest wyciek sprężonego powietrza, który może prowadzić do znacznych strat energii oraz obniżenia efektywności działania systemu. Wyciek może występować w różnych miejscach, takich jak połączenia rur czy uszczelki, dlatego regularne kontrole stanu technicznego są niezbędne do ich eliminacji. Innym powszechnym problemem jest zanieczyszczenie sprężonego powietrza, które może powodować uszkodzenia elementów układu oraz obniżać jakość wykonywanych prac. Aby temu zapobiec, należy stosować odpowiednie filtry oraz osuszacze powietrza. Problemy z ciśnieniem roboczym to kolejny istotny temat – zarówno zbyt niskie, jak i zbyt wysokie ciśnienie mogą prowadzić do awarii sprzętu lub niewłaściwego działania maszyn. Regularne monitorowanie ciśnienia oraz jego dostosowywanie do wymagań danego procesu jest kluczowe dla prawidłowego funkcjonowania układu pneumatycznego.
Jakie są przyszłościowe kierunki rozwoju technologii pneumatycznych
Przemysł pneumatyczny przechodzi dynamiczne zmiany związane z postępem technologicznym oraz rosnącymi wymaganiami rynku. Wśród przyszłościowych kierunków rozwoju technologii pneumatycznych można wymienić coraz większą automatyzację procesów produkcyjnych. Dzięki zastosowaniu zaawansowanych algorytmów sztucznej inteligencji oraz uczenia maszynowego możliwe będzie optymalizowanie pracy maszyn w czasie rzeczywistym oraz przewidywanie potencjalnych awarii zanim one wystąpią. To podejście przyczyni się do zwiększenia efektywności i niezawodności systemów pneumatycznych. Kolejnym ważnym trendem jest rozwój materiałów o wysokiej wytrzymałości i odporności na ekstremalne warunki pracy, co pozwoli na produkcję bardziej trwałych i niezawodnych komponentów pneumatycznych. Warto również zwrócić uwagę na rosnącą popularność rozwiązań ekologicznych – technologie związane z recyklingiem sprężonego powietrza oraz zmniejszeniem zużycia energii stają się coraz bardziej istotne w kontekście ochrony środowiska. Dodatkowo integracja systemów pneumatycznych z technologiami IoT umożliwi zdalne monitorowanie stanu urządzeń oraz zarządzanie nimi poprzez aplikacje mobilne czy platformy internetowe.
Jakie są najważniejsze standardy bezpieczeństwa dla maszyn pneumatycznych
Bezpieczeństwo użytkowania maszyn pneumatycznych jest kluczowym zagadnieniem zarówno dla pracowników, jak i dla samego przedsiębiorstwa. Istnieje szereg standardów oraz norm dotyczących bezpieczeństwa tych urządzeń, które powinny być przestrzegane podczas ich projektowania oraz eksploatacji. Przede wszystkim ważne jest zapewnienie odpowiedniej wentylacji pomieszczeń, w których znajdują się maszyny pneumatyczne, aby uniknąć gromadzenia się niebezpiecznych gazów czy oparów sprężonego powietrza. Kolejnym istotnym aspektem jest stosowanie zabezpieczeń mechanicznych takich jak osłony czy blokady dostępu do ruchomych części maszyn – to pozwala na minimalizowanie ryzyka urazów podczas pracy z urządzeniami pneumatycznymi. Regularne szkolenie pracowników dotyczące zasad BHP oraz obsługi maszyn również ma kluczowe znaczenie dla bezpieczeństwa pracy – dobrze przeszkolony personel potrafi skutecznie reagować w sytuacjach awaryjnych oraz unikać potencjalnych zagrożeń.
Jakie są koszty eksploatacji maszyn pneumatycznych
Koszty eksploatacji maszyn pneumatycznych są istotnym czynnikiem wpływającym na decyzje inwestycyjne przedsiębiorstw wykorzystujących tę technologię w swojej działalności. Koszty te obejmują zarówno wydatki związane z zakupem sprzętu oraz jego instalacją, jak i bieżące koszty operacyjne związane z użytkowaniem urządzeń. Na początku warto zwrócić uwagę na koszty zakupu kompresorów oraz innych komponentów układu pneumatycznego – ceny te mogą się znacznie różnić w zależności od producenta oraz specyfiki zastosowania urządzeń.