Budowa maszyn przemysłowych na zamówienie to proces, który wymaga starannego planowania oraz realizacji. Kluczowym etapem…
Budowa maszyn roboczych to złożony proces, który wymaga uwzględnienia wielu kluczowych elementów. W pierwszej kolejności należy zwrócić uwagę na konstrukcję mechaniczną, która stanowi podstawę każdej maszyny. Elementy takie jak ramy, osie czy wały muszą być odpowiednio zaprojektowane, aby zapewnić stabilność i wytrzymałość całej konstrukcji. Kolejnym istotnym aspektem jest napęd, który może być realizowany za pomocą silników elektrycznych, spalinowych lub hydraulicznych. Wybór odpowiedniego źródła napędu ma ogromne znaczenie dla efektywności pracy maszyny oraz jej wydajności. Nie można zapomnieć o systemach sterowania, które pozwalają na precyzyjne zarządzanie pracą maszyny. Nowoczesne maszyny często wyposażone są w zaawansowane technologie automatyzacji, co zwiększa ich funkcjonalność i umożliwia zdalne sterowanie. Ostatnim, ale nie mniej ważnym elementem są materiały użyte do budowy maszyn, które powinny charakteryzować się wysoką odpornością na zużycie oraz korozję.
Jakie są najczęstsze zastosowania maszyn roboczych w przemyśle
Maszyny robocze znajdują szerokie zastosowanie w różnych branżach przemysłowych, co czyni je niezbędnymi narzędziami w codziennej produkcji. W przemyśle budowlanym maszyny takie jak koparki, ładowarki czy dźwigi odgrywają kluczową rolę w realizacji projektów budowlanych. Dzięki nim możliwe jest szybkie i efektywne wykonywanie prac ziemnych oraz transport materiałów budowlanych. W sektorze produkcyjnym maszyny robocze są wykorzystywane do obróbki metali, tworzyw sztucznych oraz innych materiałów. W tym kontekście szczególnie ważne są tokarki, frezarki oraz prasy, które umożliwiają precyzyjne formowanie i łączenie elementów. W rolnictwie maszyny takie jak traktory czy kombajny znacznie ułatwiają prace polowe oraz zbiór plonów, co przekłada się na zwiększenie wydajności produkcji rolnej. W logistyce i magazynowaniu maszyny robocze pomagają w automatyzacji procesów transportowych oraz składowania towarów, co przyczynia się do optymalizacji kosztów operacyjnych.
Jakie innowacje technologiczne wpływają na budowę maszyn roboczych
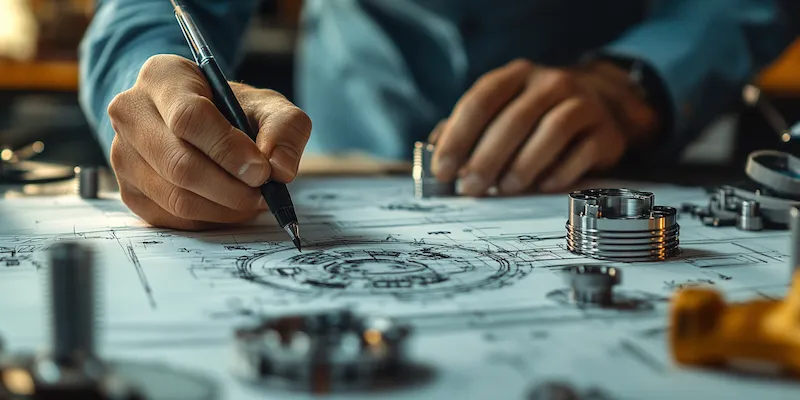
W ostatnich latach obserwuje się dynamiczny rozwój technologii, który ma istotny wpływ na budowę maszyn roboczych. Innowacje te obejmują zarówno nowe materiały, jak i zaawansowane systemy sterowania oraz automatyzacji. Przykładem mogą być kompozyty o wysokiej wytrzymałości, które zastępują tradycyjne metale w konstrukcjach maszyn, co pozwala na zmniejszenie ich wagi przy jednoczesnym zachowaniu wysokiej odporności na uszkodzenia. Również technologie druku 3D zdobywają coraz większą popularność w produkcji części zamiennych do maszyn roboczych, co umożliwia szybsze prototypowanie oraz redukcję kosztów produkcji. W zakresie automatyzacji warto wspomnieć o zastosowaniu sztucznej inteligencji oraz robotyki w procesach produkcyjnych, co pozwala na zwiększenie precyzji i efektywności pracy maszyn. Systemy IoT (Internet of Things) również zaczynają odgrywać kluczową rolę w monitorowaniu stanu technicznego maszyn oraz przewidywaniu awarii dzięki analizie danych w czasie rzeczywistym.
Jakie są wyzwania związane z budową nowoczesnych maszyn roboczych
Budowa nowoczesnych maszyn roboczych wiąże się z szeregiem wyzwań, które muszą być skutecznie adresowane przez inżynierów i projektantów. Jednym z głównych problemów jest konieczność dostosowania się do szybko zmieniających się norm i regulacji dotyczących bezpieczeństwa oraz ochrony środowiska. Wprowadzenie nowych standardów może wymagać znacznych zmian w projektach maszyn oraz ich komponentów, co wiąże się z dodatkowymi kosztami i czasem potrzebnym na wdrożenie zmian. Kolejnym wyzwaniem jest integracja zaawansowanych technologii z istniejącymi systemami produkcyjnymi. Firmy muszą inwestować w szkolenia pracowników oraz modernizację infrastruktury, aby móc skutecznie wykorzystać potencjał nowoczesnych rozwiązań technologicznych. Ponadto rosnąca konkurencja na rynku wymusza ciągłe doskonalenie produktów oraz poszukiwanie innowacyjnych rozwiązań, co stawia przed producentami dodatkowe wymagania dotyczące jakości i efektywności kosztowej.
Jakie są kluczowe aspekty bezpieczeństwa w budowie maszyn roboczych
Bezpieczeństwo w budowie maszyn roboczych jest jednym z najważniejszych aspektów, które muszą być brane pod uwagę na każdym etapie projektowania i produkcji. W pierwszej kolejności należy zwrócić uwagę na odpowiednie normy i regulacje, które definiują wymagania dotyczące bezpieczeństwa maszyn. Przykładem mogą być dyrektywy Unii Europejskiej, takie jak dyrektywa maszynowa, która określa minimalne wymagania dotyczące bezpieczeństwa i zdrowia użytkowników. Kluczowym elementem jest także przeprowadzanie analizy ryzyka, która pozwala zidentyfikować potencjalne zagrożenia związane z użytkowaniem maszyny oraz wdrożyć odpowiednie środki ochrony. W kontekście konstrukcji maszyn niezwykle istotne jest zastosowanie odpowiednich osłon, zabezpieczeń oraz systemów awaryjnego zatrzymania, które mają na celu minimalizację ryzyka wypadków. Również ergonomia odgrywa ważną rolę w projektowaniu maszyn roboczych, ponieważ dobrze zaprojektowane stanowiska pracy mogą znacząco wpłynąć na komfort i bezpieczeństwo operatorów.
Jakie są trendy w rozwoju technologii budowy maszyn roboczych
W ostatnich latach można zaobserwować wiele interesujących trendów w rozwoju technologii budowy maszyn roboczych, które mają na celu zwiększenie ich wydajności oraz funkcjonalności. Jednym z najważniejszych trendów jest automatyzacja procesów produkcyjnych, która pozwala na zwiększenie efektywności pracy oraz redukcję kosztów operacyjnych. Wprowadzenie robotów przemysłowych do linii produkcyjnych umożliwia precyzyjne wykonywanie powtarzalnych zadań, co przekłada się na wyższą jakość produktów. Kolejnym istotnym trendem jest rozwój technologii cyfrowych, takich jak sztuczna inteligencja czy analiza danych, które pozwalają na optymalizację procesów produkcyjnych oraz przewidywanie awarii maszyn. Dzięki zastosowaniu systemów monitorowania w czasie rzeczywistym możliwe jest zbieranie danych dotyczących pracy maszyn i ich analizy, co pozwala na szybsze podejmowanie decyzji oraz lepsze zarządzanie zasobami. Również rozwój technologii ekologicznych staje się coraz bardziej widoczny w branży budowy maszyn roboczych. Producenci starają się tworzyć maszyny o niższym zużyciu energii oraz mniejszym wpływie na środowisko naturalne, co wpisuje się w globalne dążenie do zrównoważonego rozwoju.
Jakie są najważniejsze wyzwania związane z konserwacją maszyn roboczych
Konserwacja maszyn roboczych to kluczowy element zapewnienia ich długotrwałej i efektywnej pracy. Wyzwania związane z konserwacją mogą być różnorodne i często wymagają specjalistycznej wiedzy oraz umiejętności. Jednym z głównych problemów jest konieczność regularnego przeprowadzania przeglądów technicznych oraz wymiany zużytych części, co wiąże się z dodatkowymi kosztami dla przedsiębiorstw. Często zdarza się również, że brak odpowiednich procedur konserwacyjnych prowadzi do przedwczesnego zużycia maszyn lub ich awarii, co może generować straty finansowe związane z przestojami w produkcji. Kolejnym wyzwaniem jest dostępność części zamiennych do starszych modeli maszyn, których produkcja została zakończona. W takich przypadkach konieczne może być poszukiwanie alternatywnych rozwiązań lub modyfikacja istniejących komponentów. Również szkolenie personelu odpowiedzialnego za konserwację maszyn jest niezwykle istotne, ponieważ niewłaściwe procedury mogą prowadzić do uszkodzeń sprzętu lub zagrożeń dla bezpieczeństwa pracowników.
Jakie są różnice między tradycyjnymi a nowoczesnymi metodami budowy maszyn roboczych
Budowa maszyn roboczych ewoluowała na przestrzeni lat, a różnice między tradycyjnymi a nowoczesnymi metodami są znaczące i wpływają na cały proces projektowania oraz produkcji. Tradycyjne metody opierały się głównie na ręcznych technikach obróbczych oraz prostych narzędziach mechanicznych, co często prowadziło do dłuższych czasów produkcji i większej liczby błędów ludzkich. Nowoczesne metody korzystają z zaawansowanych technologii takich jak CAD (Computer-Aided Design), które umożliwiają precyzyjne projektowanie elementów maszyny oraz symulacje ich działania przed rozpoczęciem produkcji. Dzięki temu możliwe jest wykrycie potencjalnych problemów już na etapie projektowania, co znacznie zwiększa efektywność całego procesu budowy. Kolejną różnicą jest zastosowanie nowoczesnych materiałów kompozytowych oraz lekkich stopów metali, które charakteryzują się wysoką wytrzymałością przy jednoczesnym zmniejszeniu wagi konstrukcji. W kontekście produkcji warto również wspomnieć o automatyzacji procesów montażowych oraz wykorzystaniu robotyki, co pozwala na zwiększenie wydajności i redukcję kosztów pracy.
Jakie są kluczowe czynniki wpływające na wybór technologii budowy maszyn roboczych
Wybór technologii budowy maszyn roboczych to proces skomplikowany i zależny od wielu czynników, które muszą być starannie analizowane przez inżynierów i menedżerów projektów. Pierwszym czynnikiem jest specyfika zastosowania maszyny – różne branże mają odmienne wymagania dotyczące wydajności, precyzji czy trwałości urządzeń. Na przykład maszyny wykorzystywane w przemyśle ciężkim muszą charakteryzować się dużą odpornością na ekstremalne warunki pracy, podczas gdy urządzenia stosowane w precyzyjnej obróbce metali muszą zapewniać najwyższą dokładność wykonania. Kolejnym czynnikiem są koszty – zarówno początkowe inwestycje związane z zakupem technologii, jak i późniejsze koszty eksploatacji i konserwacji. Firmy często muszą balansować między jakością a ceną technologii, aby osiągnąć optymalny stosunek kosztów do korzyści. Również dostępność materiałów oraz komponentów ma znaczenie – wybór technologii powinien uwzględniać lokalny rynek dostawców oraz możliwości logistyczne przedsiębiorstwa.
Jakie są przyszłe kierunki rozwoju budowy maszyn roboczych
Przyszłość budowy maszyn roboczych zapowiada się niezwykle interesująco dzięki dynamicznemu rozwojowi technologii oraz zmieniającym się potrzebom rynku. Jednym z kluczowych kierunków rozwoju będzie dalsza automatyzacja procesów produkcyjnych, która ma na celu zwiększenie wydajności oraz redukcję kosztów operacyjnych. Zastosowanie robotyzacji w różnych etapach produkcji stanie się standardem, co pozwoli na osiągnięcie większej precyzji i powtarzalności procesów. Kolejnym ważnym trendem będzie rozwój inteligentnych systemów zarządzania produkcją opartych na sztucznej inteligencji i analizie danych big data.