Wybór odpowiedniej destylarki do rozpuszczalników jest kluczowy dla uzyskania wysokiej jakości produktów. Na rynku dostępnych…
Destylacja rozpuszczalników to proces, który polega na oddzieleniu składników mieszaniny na podstawie różnicy ich temperatur wrzenia. Jest to jedna z najstarszych i najczęściej stosowanych metod separacji substancji chemicznych. W praktyce, proces ten wymaga zastosowania odpowiednich urządzeń, takich jak kolumna destylacyjna, która umożliwia wielokrotne skraplanie i parowanie substancji, co zwiększa czystość uzyskiwanego produktu. W pierwszym etapie destylacji rozpuszczalników, mieszanina jest podgrzewana do momentu, w którym składnik o najniższej temperaturze wrzenia zaczyna parować. Para następnie przechodzi przez chłodnicę, gdzie skrapla się i zbiera w osobnym naczyniu. Kluczowym elementem tego procesu jest kontrola temperatury oraz ciśnienia, które mają istotny wpływ na efektywność separacji.
Jakie są rodzaje destylacji stosowane w laboratoriach
W laboratoriach chemicznych wyróżnia się kilka rodzajów destylacji, które różnią się od siebie zarówno zastosowaniem, jak i techniką wykonania. Najpopularniejsze z nich to destylacja prosta, frakcyjna oraz azeotropowa. Destylacja prosta jest najczęściej stosowana do separacji cieczy o znacznie różniących się temperaturach wrzenia. Proces ten jest stosunkowo szybki i prosty, jednak nie zawsze zapewnia wysoką czystość uzyskanego produktu. Z kolei destylacja frakcyjna jest bardziej zaawansowaną metodą, która pozwala na oddzielenie składników o zbliżonych temperaturach wrzenia dzięki zastosowaniu kolumny frakcyjnej. Dzięki temu możliwe jest uzyskanie wyższej czystości rozdzielanych substancji. Destylacja azeotropowa natomiast jest stosowana w przypadku cieczy tworzących azeotrop, czyli mieszanin o stałej temperaturze wrzenia, które zachowują swoje proporcje podczas parowania.
Jakie są zastosowania destylacji rozpuszczalników w przemyśle
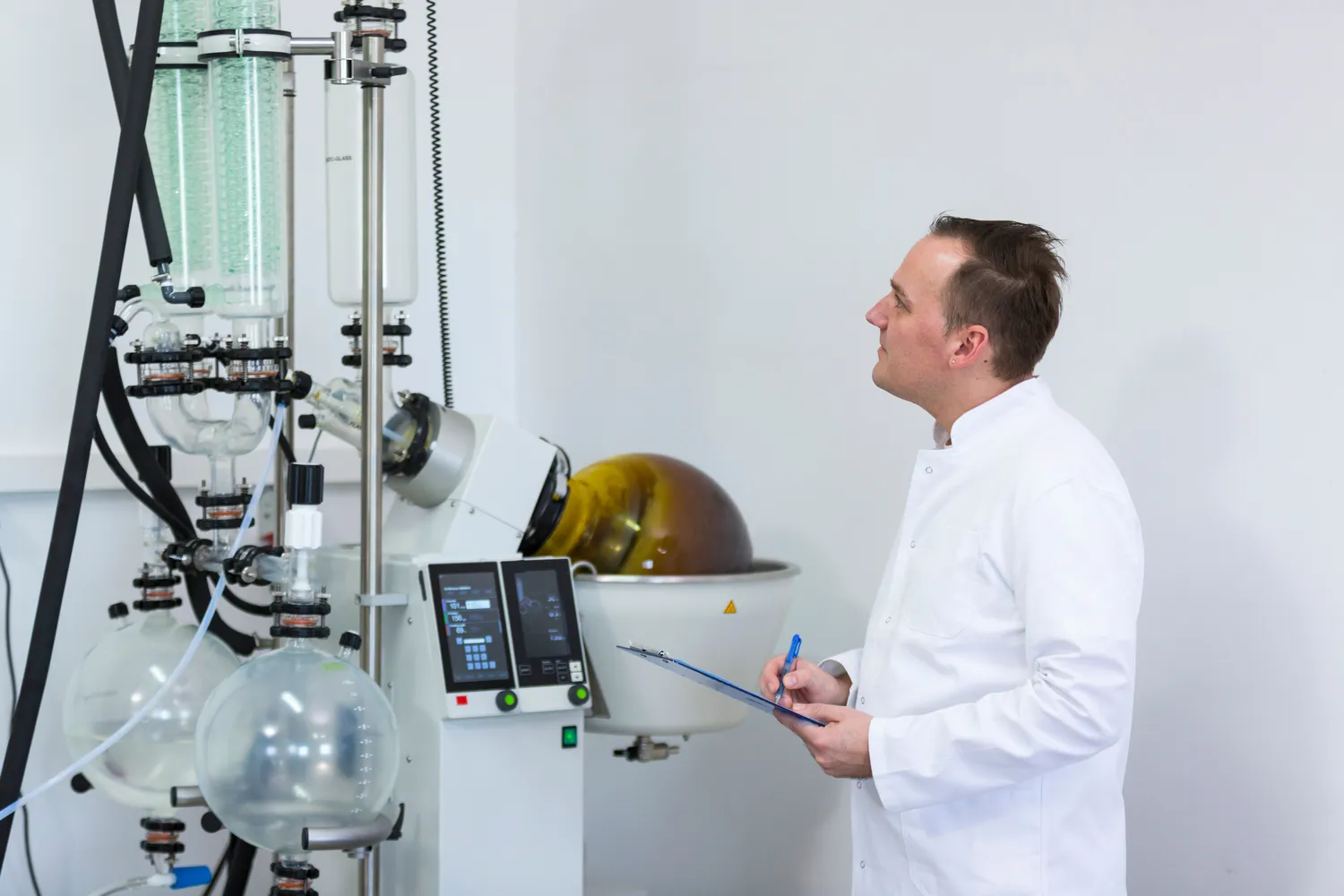
Destylacja rozpuszczalników ma szerokie zastosowanie w różnych gałęziach przemysłu chemicznego oraz farmaceutycznego. W przemyśle petrochemicznym proces ten jest kluczowy dla produkcji paliw oraz innych produktów naftowych. Dzięki destylacji frakcyjnej możliwe jest oddzielenie poszczególnych frakcji ropy naftowej, takich jak benzyna, olej napędowy czy parafina. W przemyśle farmaceutycznym destylacja odgrywa istotną rolę w oczyszczaniu substancji czynnych oraz rozpuszczalników używanych do produkcji leków. Czystość tych substancji ma kluczowe znaczenie dla bezpieczeństwa i skuteczności farmaceutyków. Ponadto destylacja znajduje zastosowanie w produkcji alkoholi oraz napojów spirytusowych, gdzie proces ten pozwala na uzyskanie wysokoprocentowego alkoholu poprzez wielokrotne skraplanie i parowanie.
Jakie są zalety i wady procesu destylacji rozpuszczalników
Proces destylacji rozpuszczalników ma swoje zalety oraz wady, które warto rozważyć przed jego zastosowaniem. Do głównych zalet należy zaliczyć efektywność separacji składników oraz możliwość uzyskania wysokiej czystości produktów końcowych. Dodatkowo proces ten jest stosunkowo prosty do zrealizowania i można go dostosować do różnych typów mieszanin chemicznych poprzez modyfikację parametrów operacyjnych takich jak temperatura czy ciśnienie. Niemniej jednak istnieją także pewne ograniczenia związane z tym procesem. Przede wszystkim niektóre substancje mogą ulegać rozkładowi w wysokich temperaturach, co może prowadzić do utraty cennych składników lub powstawania niepożądanych produktów ubocznych. Ponadto destylacja wymaga znacznych nakładów energetycznych oraz odpowiednich urządzeń laboratoryjnych lub przemysłowych, co może zwiększać koszty produkcji.
Jakie są najczęstsze błędy podczas destylacji rozpuszczalników
Podczas przeprowadzania procesu destylacji rozpuszczalników, istnieje wiele pułapek, które mogą prowadzić do nieefektywności lub wręcz całkowitych niepowodzeń. Jednym z najczęstszych błędów jest niewłaściwe ustawienie temperatury. Zbyt niska temperatura może spowodować, że składniki o wyższej temperaturze wrzenia nie będą się parować, co skutkuje niepełnym oddzieleniem substancji. Z drugiej strony, zbyt wysoka temperatura może prowadzić do rozkładu termicznego substancji, co z kolei wpływa na jakość uzyskanego produktu. Kolejnym istotnym błędem jest niewłaściwe dobranie kolumny destylacyjnej. W przypadku mieszanin o zbliżonych temperaturach wrzenia, użycie kolumny o niewłaściwej wysokości lub liczbie teoretycznych półek może znacząco obniżyć efektywność separacji. Należy również pamiętać o odpowiedniej konserwacji sprzętu, ponieważ zanieczyszczenia w urządzeniach mogą prowadzić do kontaminacji produktów końcowych.
Jakie są nowoczesne technologie związane z destylacją rozpuszczalników
W ostatnich latach nastąpił znaczny rozwój technologii związanych z destylacją rozpuszczalników, co pozwala na zwiększenie efektywności tego procesu oraz poprawę jakości uzyskiwanych produktów. Jednym z przykładów nowoczesnych rozwiązań jest zastosowanie technologii membranowej, która umożliwia separację składników bez konieczności ich parowania i skraplania. Membrany te działają na zasadzie selektywnej permeacji, co pozwala na oddzielenie substancji na podstawie ich wielkości cząsteczkowej lub właściwości chemicznych. Innym innowacyjnym podejściem jest wykorzystanie technologii mikrofalowej do podgrzewania mieszanin, co pozwala na szybsze i bardziej równomierne ogrzewanie oraz zmniejsza ryzyko rozkładu termicznego składników. Dodatkowo, automatyzacja procesów destylacyjnych przy użyciu zaawansowanych systemów sterowania i monitorowania pozwala na precyzyjne dostosowanie parametrów operacyjnych oraz minimalizację ryzyka błędów ludzkich.
Jakie są różnice między destylacją a innymi metodami separacji
Destylacja rozpuszczalników to tylko jedna z wielu metod separacji składników mieszanin chemicznych. Istnieją inne techniki, takie jak ekstrakcja, filtracja czy chromatografia, które różnią się od siebie zasadą działania oraz zastosowaniem. Ekstrakcja polega na wykorzystaniu różnicy rozpuszczalności składników w różnych rozpuszczalnikach, co pozwala na ich oddzielenie bez konieczności podgrzewania. Jest to szczególnie przydatne w przypadku substancji termolabilnych, które mogłyby ulec degradacji podczas destylacji. Filtracja natomiast jest metodą mechaniczną, która polega na oddzieleniu ciał stałych od cieczy za pomocą odpowiednich materiałów filtracyjnych. Chociaż filtracja jest prostą i szybką metodą separacji, nie nadaje się do oddzielania składników o podobnych właściwościach chemicznych. Chromatografia to bardziej zaawansowana technika separacyjna, która opiera się na różnicy w adsorpcji składników na powierzchni materiału stacjonarnego oraz ich mobilności w fazie ruchomej.
Jakie są przyszłe kierunki badań nad destylacją rozpuszczalników
Przyszłość badań nad destylacją rozpuszczalników wydaje się obiecująca dzięki rosnącemu zainteresowaniu efektywnością energetyczną oraz ekologicznymi aspektami procesów chemicznych. Wiele zespołów badawczych koncentruje się na opracowywaniu nowych materiałów dla kolumn destylacyjnych, które mogłyby zwiększyć efektywność separacji oraz zmniejszyć zużycie energii. Badania nad zastosowaniem nanotechnologii w konstrukcji membran do separacji cieczy również stają się coraz bardziej popularne, ponieważ mogą one znacznie poprawić wydajność procesów separacyjnych. Ponadto rozwijane są nowe metody analizy danych procesowych, które pozwalają na lepsze modelowanie i optymalizację warunków pracy urządzeń destylacyjnych. W kontekście ochrony środowiska badania koncentrują się także na minimalizacji odpadów powstających podczas procesu oraz poszukiwaniu alternatywnych rozpuszczalników o mniejszym wpływie na środowisko naturalne.
Jakie są wyzwania związane z przemysłową skalą destylacji rozpuszczalników
Przemysłowa skala destylacji rozpuszczalników wiąże się z wieloma wyzwaniami technologicznymi oraz ekonomicznymi, które muszą być uwzględnione podczas projektowania i eksploatacji zakładów produkcyjnych. Jednym z głównych wyzwań jest zapewnienie odpowiedniej efektywności energetycznej procesów destylacyjnych. W przemyśle chemicznym zużycie energii stanowi istotny koszt operacyjny, dlatego konieczne jest poszukiwanie sposobów na optymalizację zużycia energii poprzez zastosowanie nowoczesnych technologii oraz recykling ciepła odpadowego. Kolejnym wyzwaniem jest kontrola jakości produktów końcowych oraz eliminacja ryzyka kontaminacji podczas procesu destylacji. W tym celu konieczne jest wdrożenie rygorystycznych procedur kontrolnych oraz regularna konserwacja sprzętu. Dodatkowo należy uwzględnić aspekty bezpieczeństwa pracy związane z obsługą substancji chemicznych oraz wysokotemperaturowymi procesami.
Jakie są najlepsze praktyki w zakresie bezpieczeństwa podczas destylacji
Bezpieczeństwo podczas procesu destylacji rozpuszczalników jest kluczowym aspektem zarówno w laboratoriach, jak i w przemyśle chemicznym. Najlepsze praktyki obejmują szereg działań mających na celu minimalizację ryzyka wystąpienia wypadków oraz zagrożeń dla zdrowia pracowników. Przede wszystkim ważne jest stosowanie odpowiednich środków ochrony osobistej takich jak rękawice ochronne, gogle czy maski przeciwgazowe w zależności od rodzaju substancji chemicznych używanych w procesie. Niezwykle istotne jest również zapewnienie odpowiedniej wentylacji pomieszczeń roboczych oraz stosowanie systemów detekcji gazów szkodliwych. Regularne szkolenia pracowników dotyczące procedur awaryjnych oraz obsługi sprzętu są niezbędne dla utrzymania wysokiego poziomu bezpieczeństwa pracy. Ponadto warto wdrożyć procedury dotyczące postępowania w przypadku awarii sprzętu lub wycieku substancji chemicznych, aby szybko reagować na potencjalne zagrożenia.