OCP, czyli zasada otwarte-zamknięte, jest jednym z kluczowych zasad programowania obiektowego, które mają na celu…
OCP, czyli organizacja cyklu produkcyjnego, to kluczowy element zarządzania procesami w różnych branżach. Działa na zasadzie optymalizacji i efektywności, co pozwala na lepsze wykorzystanie zasobów oraz skrócenie czasu produkcji. W praktyce oznacza to, że OCP umożliwia firmom planowanie i kontrolowanie wszystkich etapów produkcji, od pozyskania surowców po dostarczenie gotowego produktu do klienta. Dzięki temu przedsiębiorstwa mogą zredukować koszty, zwiększyć wydajność oraz poprawić jakość oferowanych produktów. OCP jest szczególnie istotne w branżach takich jak przemysł motoryzacyjny, elektroniczny czy spożywczy, gdzie precyzyjne zarządzanie cyklem produkcyjnym ma kluczowe znaczenie dla konkurencyjności na rynku.
Jakie są kluczowe elementy OCP i ich znaczenie
Kluczowe elementy OCP obejmują planowanie, harmonogramowanie oraz kontrolę procesów produkcyjnych. Planowanie to pierwszy krok w organizacji cyklu produkcyjnego, który polega na określeniu celów oraz zasobów potrzebnych do ich osiągnięcia. W tym etapie ważne jest również zidentyfikowanie potencjalnych zagrożeń oraz możliwości, które mogą wpłynąć na realizację planu. Harmonogramowanie natomiast polega na ustaleniu kolejności wykonywania poszczególnych zadań oraz przypisaniu odpowiednich zasobów do każdego z nich. To pozwala na efektywne wykorzystanie czasu i minimalizację przestojów w produkcji. Kontrola procesów to ostatni etap OCP, który polega na monitorowaniu postępów oraz wprowadzaniu ewentualnych korekt w przypadku wystąpienia problemów. Wszystkie te elementy są ze sobą ściśle powiązane i mają kluczowe znaczenie dla sukcesu organizacji cyklu produkcyjnego.
Jakie korzyści płyną z wdrożenia OCP w firmie
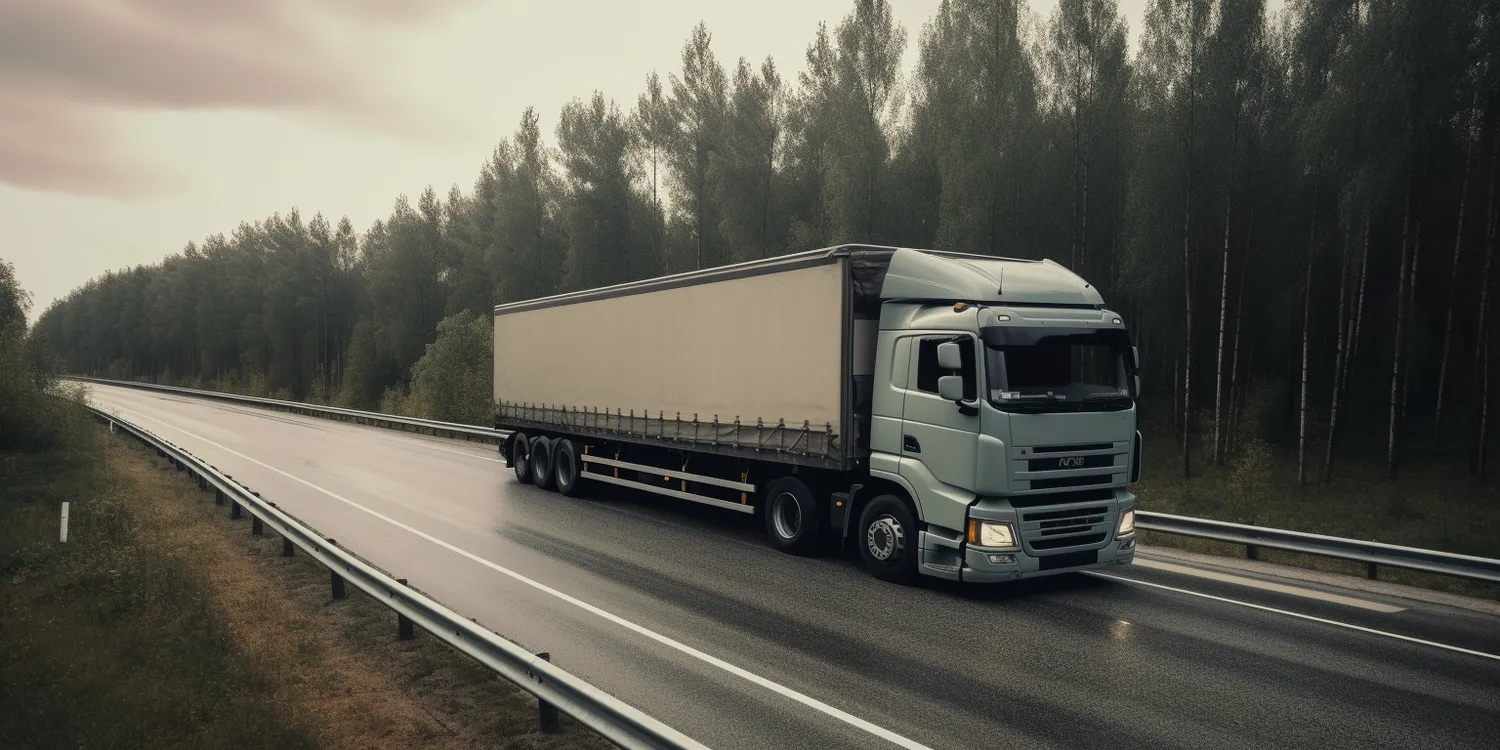
Wdrożenie OCP w firmie niesie ze sobą szereg korzyści, które mogą znacząco wpłynąć na jej rozwój i konkurencyjność. Przede wszystkim pozwala na zwiększenie efektywności procesów produkcyjnych poprzez lepsze zarządzanie zasobami oraz czasem pracy. Dzięki temu przedsiębiorstwa mogą obniżyć koszty operacyjne oraz zwiększyć rentowność. Kolejną korzyścią jest poprawa jakości produktów, ponieważ OCP umożliwia dokładniejsze monitorowanie każdego etapu produkcji oraz identyfikację potencjalnych problemów zanim staną się one poważnymi przeszkodami. Warto również zwrócić uwagę na zwiększenie satysfakcji klientów, ponieważ szybsza realizacja zamówień oraz lepsza jakość produktów przekładają się na pozytywne doświadczenia zakupowe. Dodatkowo wdrożenie OCP sprzyja innowacjom, ponieważ organizacje stają się bardziej otwarte na zmiany i nowe rozwiązania technologiczne.
Jakie wyzwania mogą napotkać firmy przy wdrażaniu OCP
Wdrażanie OCP wiąże się również z pewnymi wyzwaniami, które mogą stanowić przeszkodę dla firm pragnących skorzystać z jego zalet. Jednym z najczęstszych problemów jest opór pracowników przed zmianami, zwłaszcza jeśli są przyzwyczajeni do dotychczasowych metod pracy. W takiej sytuacji kluczowe jest odpowiednie szkolenie personelu oraz komunikacja dotycząca korzyści płynących z wdrożenia OCP. Kolejnym wyzwaniem może być konieczność inwestycji w nowoczesne technologie oraz systemy informatyczne wspierające organizację cyklu produkcyjnego. Firmy muszą także zadbać o integrację nowych rozwiązań z istniejącymi procesami, co może wymagać dodatkowego czasu i zasobów. Ponadto niektóre organizacje mogą napotkać trudności związane z analizą danych oraz podejmowaniem decyzji opartych na wynikach monitorowania procesów produkcyjnych.
Jakie narzędzia wspierają OCP i ich funkcje
Wspieranie OCP w organizacji cyklu produkcyjnego wymaga zastosowania odpowiednich narzędzi, które umożliwiają efektywne zarządzanie procesami. Do najpopularniejszych z nich należą systemy ERP, które integrują różne funkcje przedsiębiorstwa, takie jak finanse, logistyka czy zarządzanie zasobami ludzkimi. Dzięki temu możliwe jest uzyskanie pełnego obrazu działalności firmy oraz szybsze podejmowanie decyzji na podstawie danych w czasie rzeczywistym. Kolejnym istotnym narzędziem są systemy MES, które umożliwiają monitorowanie i kontrolowanie procesów produkcyjnych na poziomie zakładu. Dzięki MES można śledzić postępy produkcji, identyfikować wąskie gardła oraz optymalizować wykorzystanie maszyn i urządzeń. Warto również zwrócić uwagę na narzędzia do analizy danych, takie jak Business Intelligence, które pozwalają na przetwarzanie dużych zbiorów informacji oraz generowanie raportów wspierających podejmowanie strategicznych decyzji.
Jakie są najlepsze praktyki wdrażania OCP w firmach
Wdrażanie OCP w firmach wymaga zastosowania najlepszych praktyk, które zwiększą szanse na sukces tego procesu. Przede wszystkim kluczowe jest zaangażowanie wszystkich pracowników w proces zmian, co można osiągnąć poprzez organizację szkoleń oraz warsztatów dotyczących OCP. Ważne jest także stworzenie zespołu projektowego odpowiedzialnego za wdrożenie OCP, który będzie miał jasno określone cele oraz zadania. Kolejną istotną praktyką jest regularne monitorowanie postępów wdrożenia oraz dostosowywanie strategii do zmieniających się warunków rynkowych. Warto również korzystać z doświadczeń innych firm, które skutecznie wdrożyły OCP, aby uniknąć typowych błędów i wyzwań. Dobrą praktyką jest także stosowanie metodyki ciągłego doskonalenia, takiej jak Kaizen, która pozwala na systematyczne wprowadzanie usprawnień w procesach produkcyjnych.
Jakie przykłady firm skutecznie wdrożyły OCP
Na rynku istnieje wiele przykładów firm, które skutecznie wdrożyły OCP i odniosły dzięki temu znaczące korzyści. Jednym z najbardziej znanych przypadków jest Toyota, która opracowała system produkcji Just-in-Time oparty na zasadach OCP. Dzięki temu firma zdołała zredukować zapasy oraz zwiększyć elastyczność produkcji, co przyczyniło się do jej globalnego sukcesu. Innym interesującym przykładem jest firma Dell, która wykorzystuje OCP do zarządzania swoim łańcuchem dostaw oraz produkcją komputerów na zamówienie. Dzięki efektywnemu zarządzaniu cyklem produkcyjnym Dell może szybko reagować na zmieniające się potrzeby klientów oraz utrzymywać niskie koszty operacyjne. W branży spożywczej warto zwrócić uwagę na firmę Coca-Cola, która stosuje OCP do optymalizacji procesów produkcyjnych oraz dystrybucji swoich produktów na całym świecie. Dzięki temu firma może efektywnie zarządzać swoimi zasobami oraz sprostać rosnącemu popytowi na swoje napoje.
Jakie są przyszłe trendy związane z OCP i ich wpływ
Przyszłość OCP wiąże się z wieloma trendami technologicznymi i społecznymi, które mogą znacząco wpłynąć na sposób zarządzania cyklem produkcyjnym. Jednym z najważniejszych trendów jest automatyzacja procesów produkcyjnych za pomocą robotyki i sztucznej inteligencji. Dzięki tym technologiom przedsiębiorstwa będą mogły zwiększyć wydajność oraz jakość produkcji przy jednoczesnym obniżeniu kosztów pracy. Kolejnym istotnym trendem jest rozwój Internetu Rzeczy (IoT), który umożliwi zbieranie danych z maszyn i urządzeń w czasie rzeczywistym. To pozwoli na lepsze monitorowanie procesów produkcyjnych oraz szybsze podejmowanie decyzji opartych na analizie danych. Zmiany demograficzne i rosnące oczekiwania konsumentów również wpłyną na OCP, ponieważ firmy będą musiały dostosować swoje procesy do indywidualnych potrzeb klientów oraz zwiększonej konkurencji na rynku.
Jakie umiejętności są niezbędne do pracy w obszarze OCP
Osoby pracujące w obszarze OCP powinny posiadać szereg umiejętności i kompetencji niezbędnych do efektywnego zarządzania cyklem produkcyjnym. Przede wszystkim kluczowe są umiejętności analityczne, które pozwalają na interpretację danych oraz wyciąganie wniosków dotyczących efektywności procesów produkcyjnych. Wiedza z zakresu zarządzania projektami również odgrywa istotną rolę, ponieważ wdrażanie OCP często wiąże się z realizacją skomplikowanych projektów wymagających koordynacji działań różnych zespołów. Umiejętności interpersonalne są równie ważne, ponieważ skuteczne wdrożenie OCP wymaga współpracy między działami oraz zaangażowania pracowników na różnych szczeblach organizacji. Znajomość nowoczesnych technologii informacyjnych i komunikacyjnych jest niezbędna do wykorzystania narzędzi wspierających OCP oraz analizy danych.
Jakie są najczęstsze błędy przy wdrażaniu OCP i jak ich unikać
Wdrażanie OCP w firmach może napotkać na wiele pułapek, które mogą zniweczyć wysiłki związane z poprawą efektywności procesów produkcyjnych. Jednym z najczęstszych błędów jest brak odpowiedniego planowania oraz strategii wdrożenia, co prowadzi do chaotycznych działań i nieefektywnego wykorzystania zasobów. Firmy powinny dokładnie przeanalizować swoje potrzeby oraz cele przed rozpoczęciem procesu wdrażania OCP. Kolejnym błędem jest niedostateczne zaangażowanie pracowników, co może prowadzić do oporu przed zmianami oraz braku akceptacji dla nowych metod pracy. Aby tego uniknąć, warto zainwestować w szkolenia oraz komunikację wewnętrzną, która wyjaśni korzyści płynące z OCP. Inny problem to ignorowanie danych i wyników analizy, co może skutkować podejmowaniem decyzji na podstawie intuicji zamiast rzetelnych informacji. Firmy powinny regularnie monitorować postępy wdrożenia OCP oraz dostosowywać swoje działania w oparciu o uzyskane dane.